Petit-fils de Raymond Blondeau, ce jeune Suisse a repris les manettes de la fonderie familiale, à La Chaux-de-Fonds, en 2018. Il a fait du travail du bronze un art de la précision afin de proposer ses oeuvres au grand public et pour les plus grands événements sportifs, à l’instar des Jeux olympiques dont il est le fondeur officiel.
“Il y a du bruit ! Pas vrai ?” Dans son atelier, niché au cœur de La Chaux-de-Fonds, Aloïs Huguenin admire le travail de son collègue Ewan, casque anti-bruit vissé sur les oreilles, qui emploie un marteau pneumatique pour créer un moule servant à reproduire des lettres en bronze. Le bronze, ce fin alliage de cuivre et d’étain, est le quotidien de ces jeunes fondeurs suisses. Voilà six ans qu’Aloïs a repris l’entreprise familiale, la fonderie Blondeau, qui employait encore huit personnes il y a vingt ans.
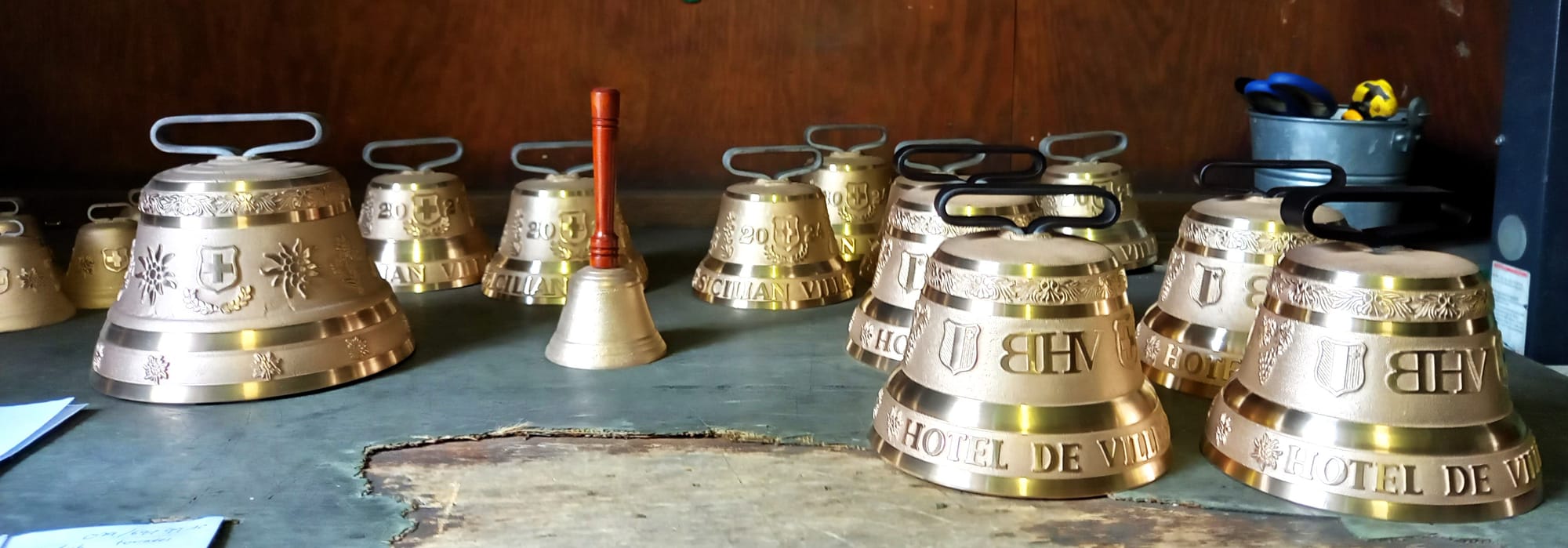
“Mon grand-père, Raymond Blondeau, produisait surtout des cloches pour l’agriculture. Il s’en fichait un peu de la qualité finale du produit : s’il y avait une impureté, cela ne dérangeait pas l’éleveur, explique-t-il en empoignant une cloche partiellement rouillée. Aujourd’hui, je fabrique vingt cloches par an pour les vaches, donc très peu. Je privilégie la qualité pour attirer d’autres clients. La fonderie reçoit, par exemple, beaucoup de visiteurs qui sont émerveillés par le bronze et la résonance qu’il produit. C’est plus cher (entre 60 et 300 euros) que les clochettes en laiton vendues dans les boutiques souvenirs, mais c’est autre chose !”
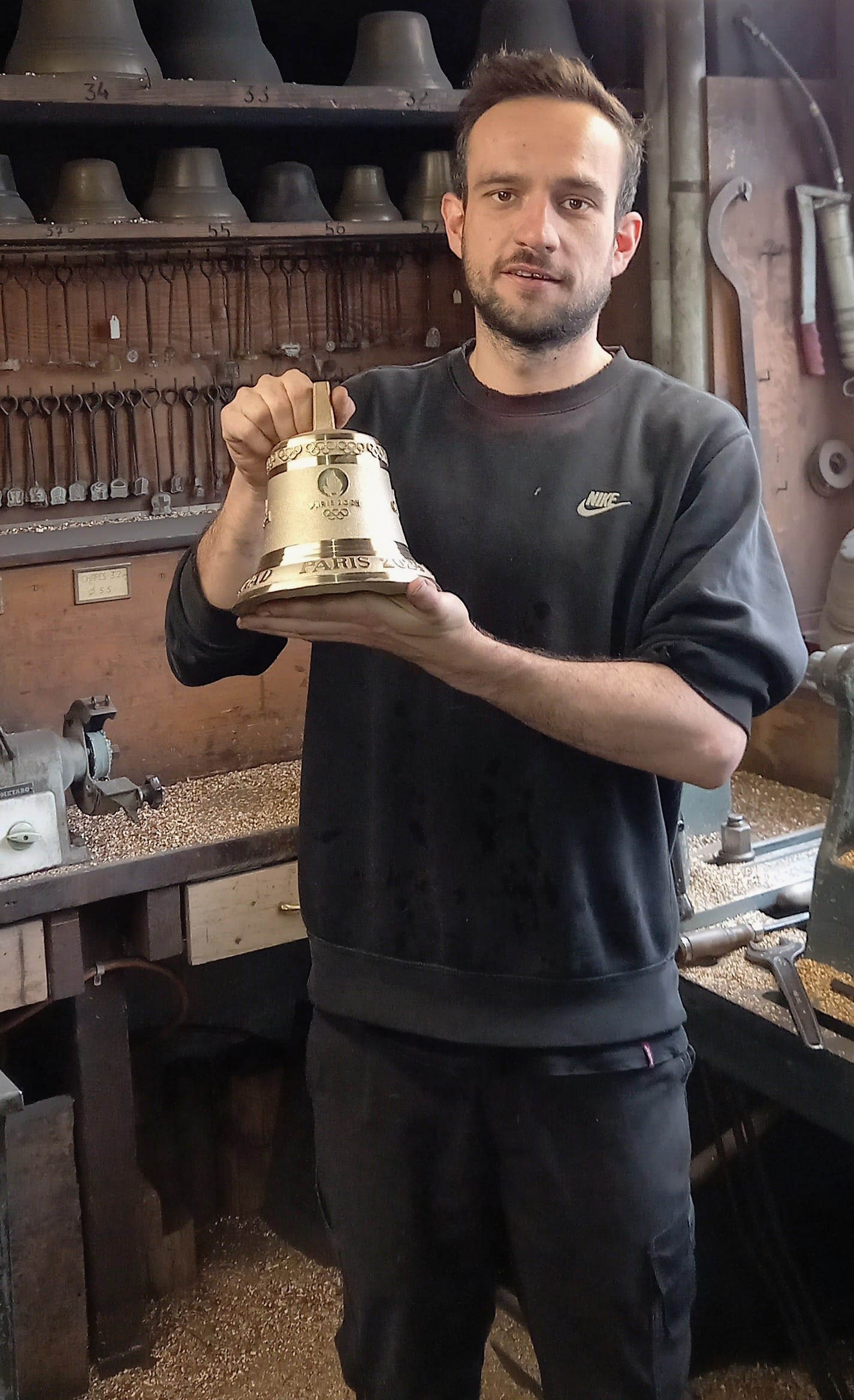
Depuis 1980, la fonderie Blondeau reçoit aussi les commandes de clients olympiques : “À l’occasion des J.O. de Moscou, l’entreprise Oméga, qui fait maintenant partie du Swatch Group, a proposé à mon grand-père de confectionner des cloches pour certaines épreuves des Jeux.” Alors que sa production était en déclin dans les années quatre-vingt, la fonderie retrouve un second souffle et une notoriété en participant, même modestement, à ce grand événement quadriennal.
“Cette année, R.T.S. et TF1 ont réalisé des reportages sur les cloches qui vont servir aux J.O. de Paris. Il y a aussi l’A.F.P. qui nous a rendu visite, donc je pense que des gens du monde entier ont pu voir notre travail”, souligne Aloïs en songeant à ses devanciers qui n’ont pas eu la chance de plastronner devant les caméras. Pour les J.O. 2024, il a dû réaliser 38 cloches d’une trentaine de centimètres, ornées de disques et de flammes olympiques, que l’on entendra résonner lors des épreuves d’athlétisme ou de cyclisme sur piste. Passionné de sport, Aloïs craint de ne pas pouvoir assister aux Jeux : “J’aimerais aller les voir, car c’est tout près. J’ai demandé des places à la direction d’Oméga, mais je n’ai toujours pas eu de réponse de leur part.”
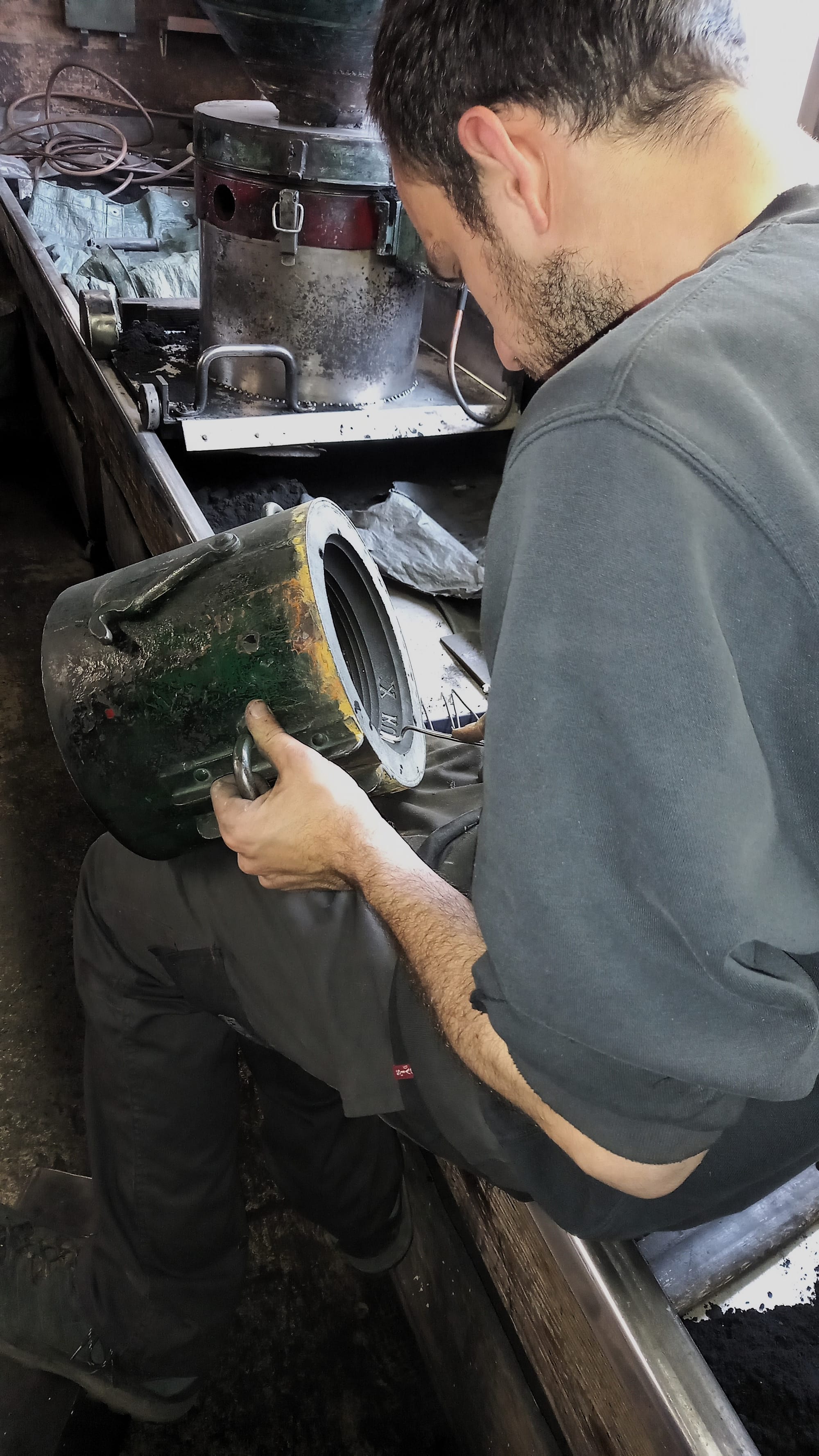
Bien qu’il ait sculpté des cloches pour des dizaines d’événements sportifs, dont le Tour de France, et même pour des champions, comme le tennisman helvète Stanislas Wawrinka, il demeure très humble. “Je n’ai pas fait d’études pour apprendre mon métier. J’ai appris sur le tas en travaillant aux côtés de mon père”, aime-t-il à préciser. Ce que lui a enseigné son paternel, ce sont des techniques utilisées depuis près de 200 ans par les fondeurs de cloches.
“Ceux qui ont créé la fonderie, des Italiens du Piémont, étamaient au départ des chaudrons. Ils n’ont pas eu beaucoup de mal à fabriquer des cloches par la suite. Leur méthode de fabrication n’a pas beaucoup évolué, le mazout remplaçant simplement aujourd’hui le coke pour faire chauffer le four”, note-t-il. La confection d’une cloche, comme celle que l’on pourra observer au Stade de France cet été, nécessite plusieurs étapes. La première et la plus technique étant le moulage : “Pour cette opération, on utilise une cloche-modèle que l’on place dans un moule en métal. On la recouvre ensuite avec une terre argileuse noire, le sable de Paris, qui va prendre la forme de la cloche au cours du séchage.”
Pour imprimer des caractères sur son ouvrage, le fondeur emploie des tiges pourvues au bout de lettres ou de décors en métal. “La précision et la concentration sont des qualités primordiales dans mon métier”, insiste Aloïs. Quand le sable devient enfin dur comme de la pierre, l’artisan peut procéder au coulage du bronze, chauffé à 1 200 °C, dans l’empreinte de la cloche. Viennent ensuite les opérations d’ébarbage, de sablage et de tournage pour adoucir les bords de l’objet, le ciseler, et le lustrer.
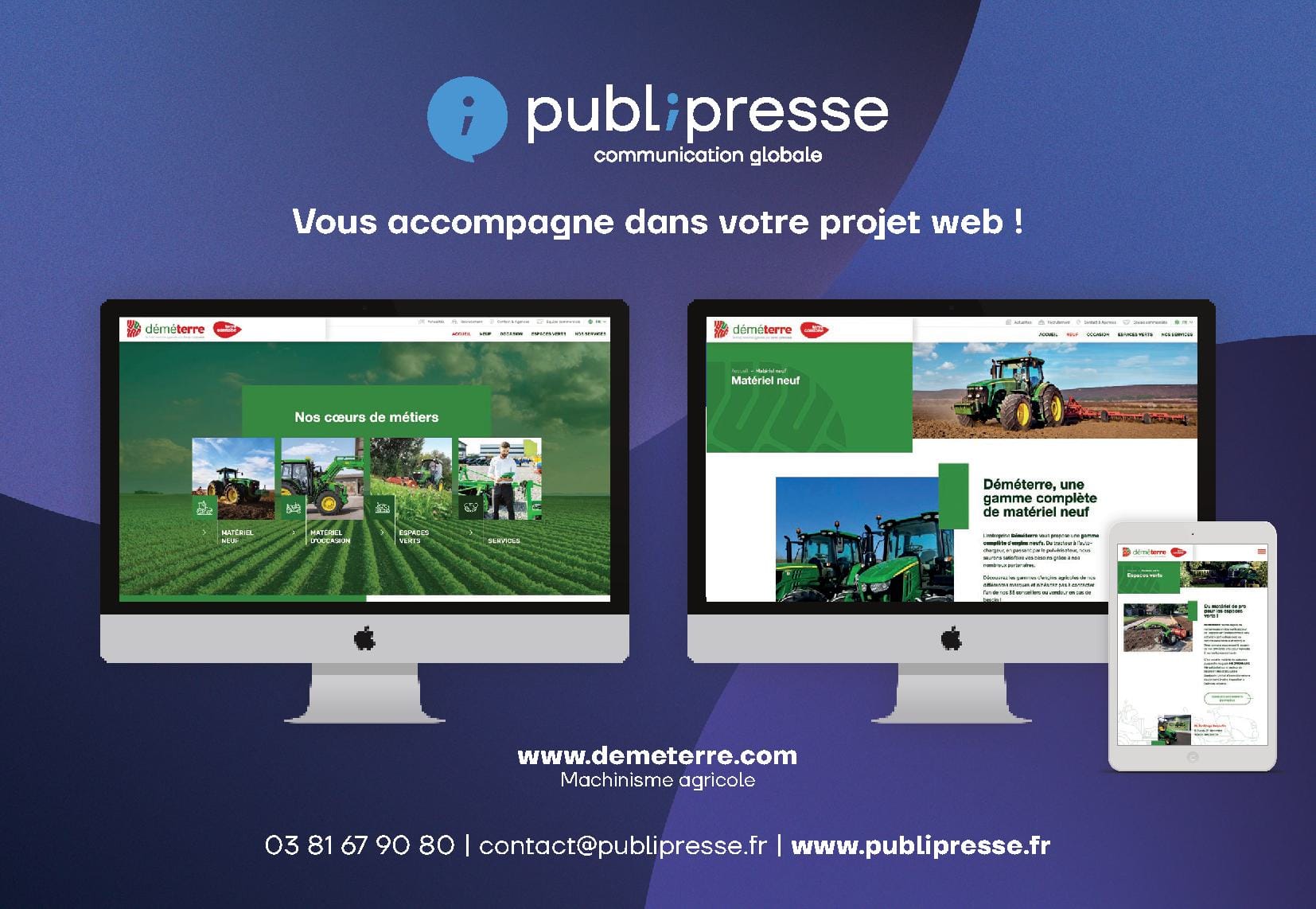
Au terme de cette laborieuse fabrication, on croirait presque que le bronze s’est mué en or. “C’est un boulot très éprouvant physiquement et dangereux : je porte une combinaison lors de la fonte et je dois faire attention lors du tournage de ne pas approcher mes mains trop près de la machine”, détaille le jeune artisan. L’attention et la minutie n’empêchent cependant pas les erreurs : “On loupe environ 10 % des cloches : c’est-à-dire que sur 30 cloches produites par mois, on en rate trois à cause d’un imprévu ou, tout bêtement, à cause de la présence d’air au moment fatidique de la coulée. Cela fait partie du métier. Je n’ai pas d’appareils de mesures, je fais tout à l’œil.”
Aloïs Huguenin est l’un des dix derniers fondeurs de cloches en Suisse. De quoi affirmer qu’il nourrit pour son métier une passion d’airain.